DTF Printing Demystified: Everything You Required to Understand About Direct-to-Film
DTF Printing Demystified: Everything You Required to Understand About Direct-to-Film
Blog Article
Ultimate Guide to DTF Printing Strategies for Sensational Textile Layouts
Getting started on the trip of understanding DTF printing strategies can open up a globe of opportunities for developing aesthetically fascinating fabric designs. In this guide, we will certainly explore the elaborate information of DTF printing, from realizing the basic essentials to unraveling advanced color methods that can elevate your layouts to brand-new heights.
Understanding DTF Printing Basics
DTF printing, a process that entails moving designs from an unique movie to textiles using warmth and stress, develops the foundation of fabric printing methods. This innovative approach permits top notch, lively styles to be seamlessly moved onto different fabrics with precision and detail. The primary step in DTF printing includes creating or picking a design that will certainly be printed onto the fabric. This design is after that published onto an unique movie utilizing a DTF printer, which uses particular dyes or pigments to make certain color accuracy and toughness.
The final outcome is a magnificent, resilient textile layout that is cleanable, adaptable, and immune to fading. Generally, recognizing the essentials of DTF printing is important for mastering this modern textile printing technique.
Choosing the Right Textile Products
Having developed the fundamental concepts of DTF printing strategies for textile styles, the following important consideration exists in selecting the appropriate textile products to enhance this innovative procedure successfully. In addition, the stretchability of these materials can suit the warm transfer process involved in DTF printing without distorting the style. By selecting the appropriate fabric products, developers can optimize the potential of DTF printing to develop sensational and resilient textile designs.
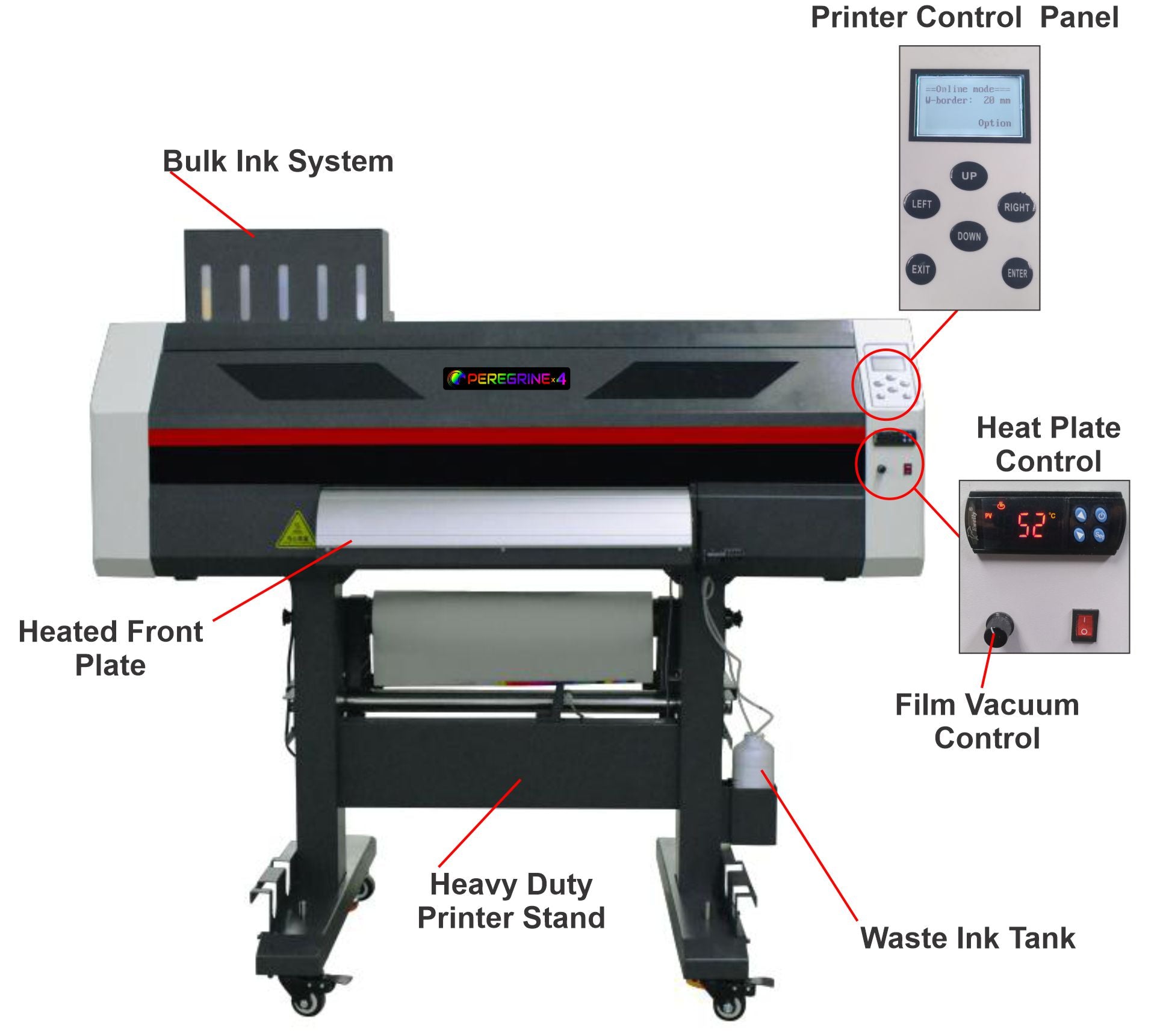
Mastering the Printing Process
To master DTF printing techniques for fabric layouts, understanding the printing procedure is important for accomplishing regular and top quality results. The printing procedure in DTF entails a number of vital actions that need accuracy and focus to information. Preparing the artwork for printing is vital. This consists of making sure the style is properly sized and placed for the fabric. Next off, the layout is printed onto an unique DTF film making use of a compatible printer with the best settings to achieve ideal shade vibrancy and clearness (DTF Printing). Once the layout is published, it is after that moved onto the material utilizing a warm press maker. The temperature level, stress, and find more information duration of warm application need to be meticulously managed to make sure proper bond of the layout to the textile. Furthermore, grasping the peeling procedure after warmth pushing is essential to prevent any type of damage to the layout or material. By honing each of these steps in the printing procedure, developers can consistently create stunning and long lasting fabric designs with DTF printing techniques.
Enhancing Designs With Shade Strategies
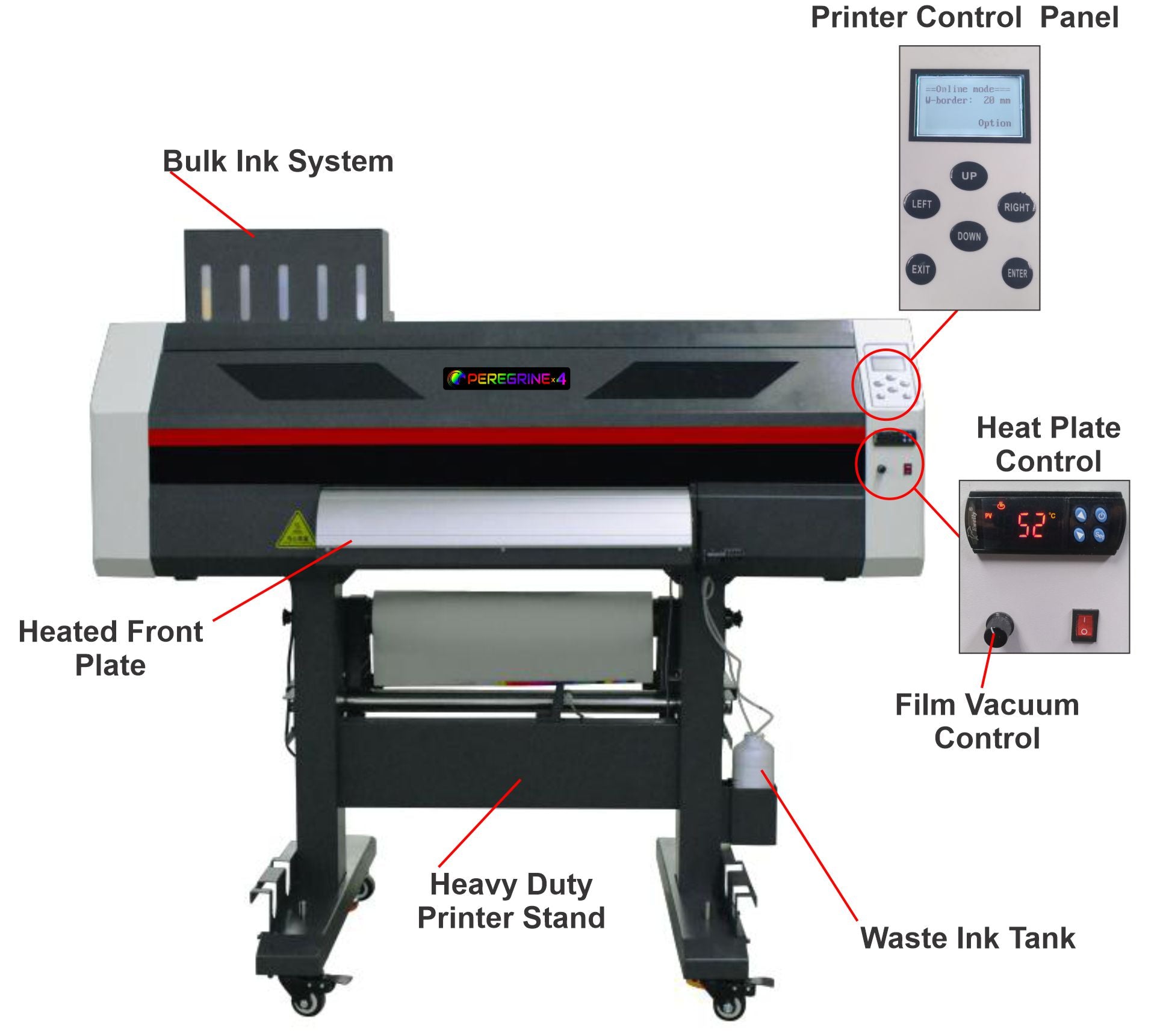
Additionally, exploring with shade slopes can bring a feeling of activity and fluidness to the layout. By mixing shades flawlessly, a slope effect can be achieved, adding a modern and dynamic touch to the textile layout. Additionally, using shade blocking strategies can produce vibrant and striking visuals by comparing different solid colors in distinct sections of the layout.
Additionally, integrating metallic or neon colors can give a attractive and unique component to the fabric design, making it stand out and exude a feeling of vibrancy. When tactically applied, these shade methods can raise the overall visual allure of textile styles, making them a lot more fascinating and unforgettable.
Troubleshooting Common DTF Printing Issues
After checking out numerous shade strategies to boost textile layouts, it is important to attend to typical DTF printing problems that might emerge during the production process. Additionally, problems with picture clarity and intensity can occur due to low-resolution images or inappropriate printing techniques. By being conscious of these typical problems and carrying out the needed troubleshooting steps, you can improve the total high quality of your DTF printed textile designs.
Final Thought
In final thought, understanding DTF printing methods is important for creating magnificent textile layouts. With practice and focus to detail, one can develop gorgeous and unique fabric designs utilizing DTF printing techniques.
Styles))))
DTF printing, a process that includes moving styles from an unique film to fabrics making use of heat and stress, forms the foundation of fabric printing methods.Having developed the foundational principles of DTF printing strategies for fabric styles, the next critical factor to consider exists in picking the proper textile materials to match this ingenious procedure properly. By choosing the best fabric materials, developers can his response make the most of the potential of DTF printing to develop spectacular and long-lasting fabric designs.
To stand out in DTF printing strategies for textile styles, grasping the printing procedure is essential for accomplishing high-grade and constant outcomes. DTF Printing. By sharpening each of these actions in the printing process, designers can regularly generate resilient and sensational fabric designs with DTF printing strategies
Report this page